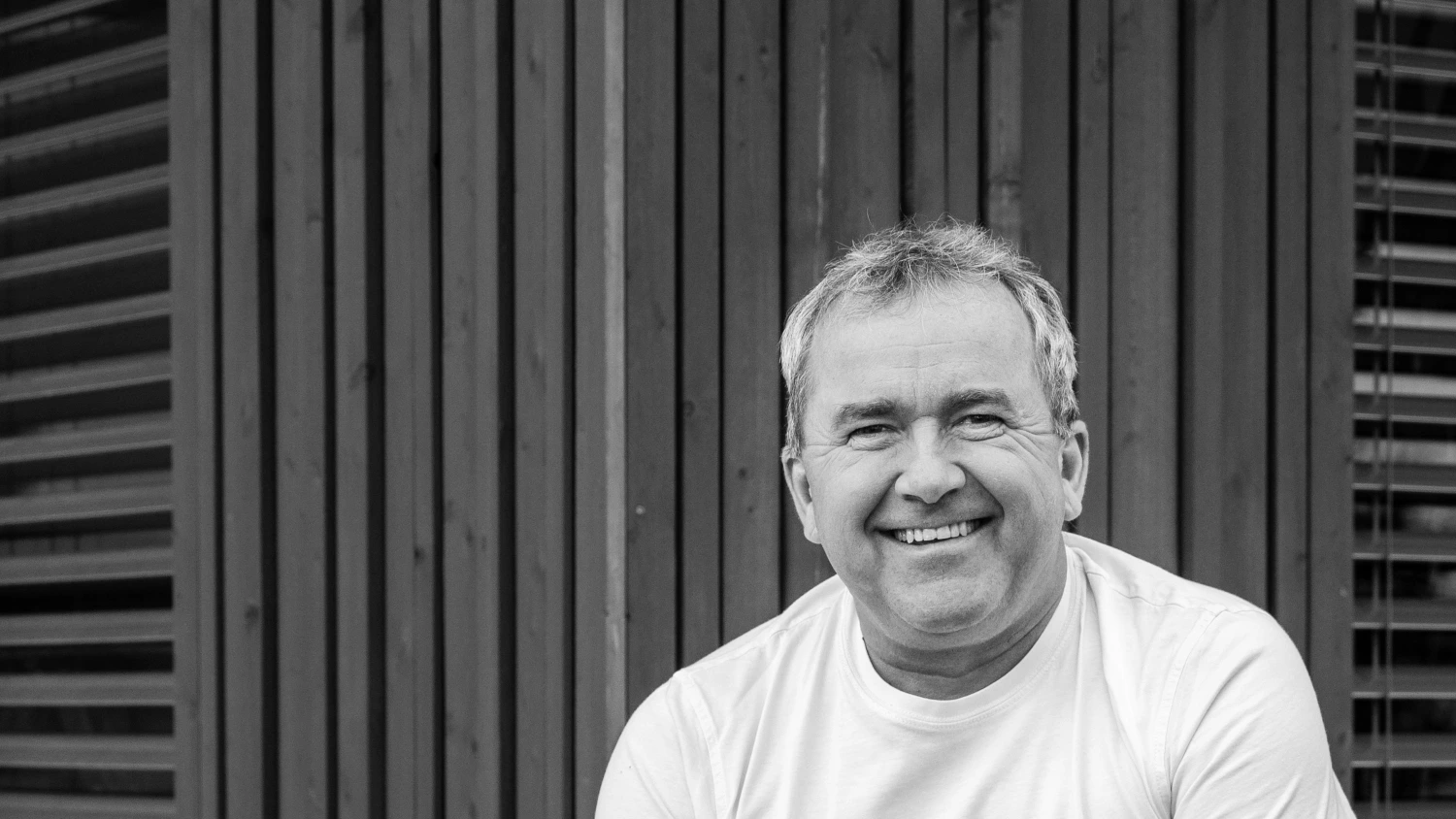
Jiří Oslizlo, Chairman of the Board of Agrop Nova talked to Property Forum about the unique properties of wood and wooden constructions and how he would like to use his life experience from abroad to help reconfigure Czech thinking and ways of building.
At the beginning of your career, you worked as a fish dealer and as an owner and CEO in the food sector. What made you change industries and enter the wood processing sector?
It was a coincidence, although I think there are no coincidences, it's just opportunities that we see or not. In the food industry, I built a company in eight years that grew from five employees to eight hundred and from zero to one billion in sales and launched, among other things, the successful Prima ice cream brand. I was disgusted by the culture of the food industry, which was disdainful of quality and the only criterion was price. This was insulting and demotivating.
In 1998 I felt tired and when the offer came to sell the company, I took it. After a six-month sabbatical, the opportunity arose to buy the factory in Ptení, which had a timeless production hall full of new machines and a great team of people. The only thing it lacked was money. I was a graduate mechanical engineer, and my domain was machinery, plus it was a place far from the big city and there was the smell of wood everywhere. Initially, I had a plan to get the company up on its feet and sell it, but it didn't happen. Over 22 years, together with a great team of people, I have built a company that is at the top of its field thanks to its exceptional craftsmanship and successfully competes with even strong European players. I really enjoy what I do, there are values other than money in this business, and I personally have many challenges ahead of me.
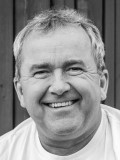
Jiří Oslizlo
Chairman of the Board
Agrop Nova
You are primarily involved in wood processing. How is the timber supply in the Czech Republic and Europe? Are you worried that there will be a shortage? That you will not have the material for your production?
Although wood is a renewable resource, it has its limits. The pressure on the yield of Czech forests due to the decline in foreign exports has been growing for the past year. The situation was further complicated by the war in Ukraine, as one of the largest importers of timber to Europe was Russia. Other sources on offer are not optimal - imports from Canada and the USA are expensive and insufficient.
The Czech Republic is able to cover its timber needs, being one of only four countries in Europe with a forest cover of around one-third. Unfortunately, we are exporting up to 75% of high-quality raw materials with zero added value, thereby degrading this golden raw material. That is why I often stress - let us treat the forest with respect and reverence because it is a place where we still have a lot to learn.
Our company is the second largest lumber processor in the Czech Republic. We process over 60,000 cubic metres of lumber and ship over 1,300,000 sqm of boards to our customers. This quantity corresponds to approximately 100,000 spruces that grow for four years on average in the Czech forests. In general, however, even if we build only with wood in the Czech Republic from now on, we have enough wood and our year's production will grow in the Czech forests in a few years. We currently use 30% export the wood in our production, we import it from Scandinavia or Ukraine, depending on the range.
To what extent is your production affected by major fires in Europe and elsewhere in the world, and by the bark beetle calamity?
We are not yet affected by the fires in Europe. Forest fires can have both positive and negative consequences, which depend on many variables. Time will tell. As far as bark beetle wood is concerned, we, like other companies, are not bothered by it. It can safely be used for timber buildings; it has purely aesthetic defects. The fact that cross-laminated timber - i.e., CLT board - has a visible and a non-visible part means that these can be hidden in the non-visible part. Any wood without rot can be used in production. Barkwood is perfectly fine in terms of strength. Worse is wood from fallen trees after a storm. It contains cracks that in a static setting can cause problems. In addition to spruce, beech wood can also be used to make boards. Its disadvantage is its higher price, and it cannot be used growing, then it twists and cracks, so it must be cut into small pieces. On the other hand, it can withstand higher static loads.
Your company focuses mainly on exports. Do you also trade within the Czech Republic?
In the beginning, we focused on Switzerland, Austria, and Germany, and later Italy, and France. Today, we have orders in many countries in Europe, Scandinavia, South Africa, and South Korea and are currently dealing with enquiries in the USA, Canada, and Australia. Exports have accounted for 85% of total sales in recent years.
Although the Czech Republic is not a superpower in timber buildings, interest in them has been growing for a long time. Orders are gradually shifting from single-family houses to the public sector, and CLT, one of the most promising construction systems in the world, has entered the game, with benefits that are in many ways unsurpassed.
We produce a unique construction system based on the CLT principle and in the Czech Republic, in addition to hundreds of family houses, commercial buildings have also been built from our NOVATOP system. These include kindergartens in Všetaty, Buková, school classrooms in Nučice, Prague-Cakovice, a community centre in Mnichovo Hradiště, the NATURA PARK environmental education centre in Pardubice, offices of the experimental building LIKO Noe, as well as guesthouses and hotel extensions. This year will also see the completion of the tallest 4-storey office building in the country, for which an enlightened investor has chosen CLT technology. The range of facilities is really very diverse. And I see a vast potential. And probably not only me, because banks are already responding with their support programmes.
I would like to use my life experience from abroad to help reconfigure Czech thinking and ways of building. Building with wood is not a necessary compromise to meet ESG criteria, but a prestige and social responsibility, a way to respect nature and ensure quality of life for future generations. We ourselves not only talk about sustainability but have really lived in harmony with it for thirty years. All production is regularly monitored by domestic and foreign independent inspection bodies and meets strict criteria for several certifications. We document accurate information on how we manage energy and water, how we manage waste, how we contribute to reducing carbon dioxide production, and emissions, and the extent to which we use sustainable materials. For each of our customers, this should be clear proof that we produce Novatop with the utmost respect for the environment.
As a company from the Czech Republic, you are successfully competing with big European players. How did you manage to gain such a position?
Quality comes first for us, and this has proven to be the strongest business argument in the long run. The exceptional craftsmanship of our products has been stable for three decades. We are one of the most modern manufacturers of large multilayer boards and CLT in Europe. From the beginning, we have been fortunate to work with the best experts in the world of timber construction. It is thanks to their innovative projects that we have learnt a lot and today we are bringing this experience from abroad to us. And they taught me one more important thing - wood must be gilded. Not to increase volume, but to increase value. That's why we innovate, to give our products the highest added value. For example, with our designer acoustic panels, we value a cube of input lumber more than five times over.
You often say that you draw inspiration for the development of your company mainly from abroad. Which country is inspiring for you in this respect and why?
We still draw most of our inspiration from Switzerland. The world's know-how in timber construction and its current cutting edge is concentrated here. It was here that I met one of the best wood engineers in the world, Hermann Blumer, who was also at the birth of our rib element, as well as several other projects we have had the honour to work on. The Swiss are generally not as strictly bound by certificates and standards as the rest of Europe and are open-minded because they have not forgotten to use common sense. Here, the simple rule is that what can be drawn and calculated can be built, which is precisely what Hermann Blumer said. And that is what motivated me to build my production hall, made of wood, of course. I want to overcome Czech prejudices and prove that wooden halls in our country are not science fiction - we have been involved in many similar projects around the world for years.
You are very much with the times in your business, and you are also introducing robotic manufacturing. How do you specifically apply it?
Innovation in production is a must. We continuously invest in production and technological equipment. The entire timber industry is still very much hardware-based, despite digitisation and robotics. My goal is to be active and invest in further product development. We must invest one million crowns (€41,5 thousand) to increase our annual production volume by one million crowns. This year we plan to commission the first fully automatic robotic line for very precise machining of thinner boards. These are also in demand, they are easier to fold, so they will make work on-site easier and faster. Sales for them will be mainly in the Alpine countries. Another challenge is modular construction, where individual modules can be used to build a whole house or just an extension. Again, the specialists from Switzerland are leading the way.
You also cooperate a lot with the University Centre. Can you describe this cooperation more?
Currently, we are actively communicating with the University Centre for Energy Efficient Buildings (UCEEB). The result of this combination of intellectual and technological potential should be a grid-based energy solution technology using hydrogen for the new production hall. In addition, we are actively working with experts and universities with a focus on spatial acoustics and fire resistance.
In the past months and years, energy prices and self-sufficiency have been much discussed here and worldwide. How is energy self-sufficiency being implemented in your company in this respect?
Our advantage is that the wood processing industry is essentially energy self-sufficient. All wood that goes through the production process is fully and completely used. The majority (about 70%) ends up in the final product. The remaining share is available in the form of various trimmings and sawdust, we press most of the sawdust into ecological fuel - briquettes. We burn the remaining 15% or so of this material in our energy furnaces to produce heat for our production and drying facilities. Our energy balance is thus significantly positive. We purchase around 6 GWh of electricity per year to support our operations, but with our ecological fuel, we produce more than 30 GWh per year. This ratio guarantees us sufficient energy security. Like most companies, we have signed contracts for the installation of two photovoltaic power plants on the roofs of our production halls with a total capacity of 1.5 MWp. So, it is the case that we intend to build our own combined heat and power generation to provide a much larger amount of energy than we consume ourselves. However, this model is not yet covered by the distribution network and legislation is not ready for this distribution system. In addition, we are cooperating with the Czech Technical University in Prague on the energy solution for the planned modular production hall. Here we want to apply, for the first time, the production and subsequent combustion of green hydrogen as a seasonal storage of solar energy. Energy self-sufficiency is another one of the measurable criteria of much-touted sustainability.