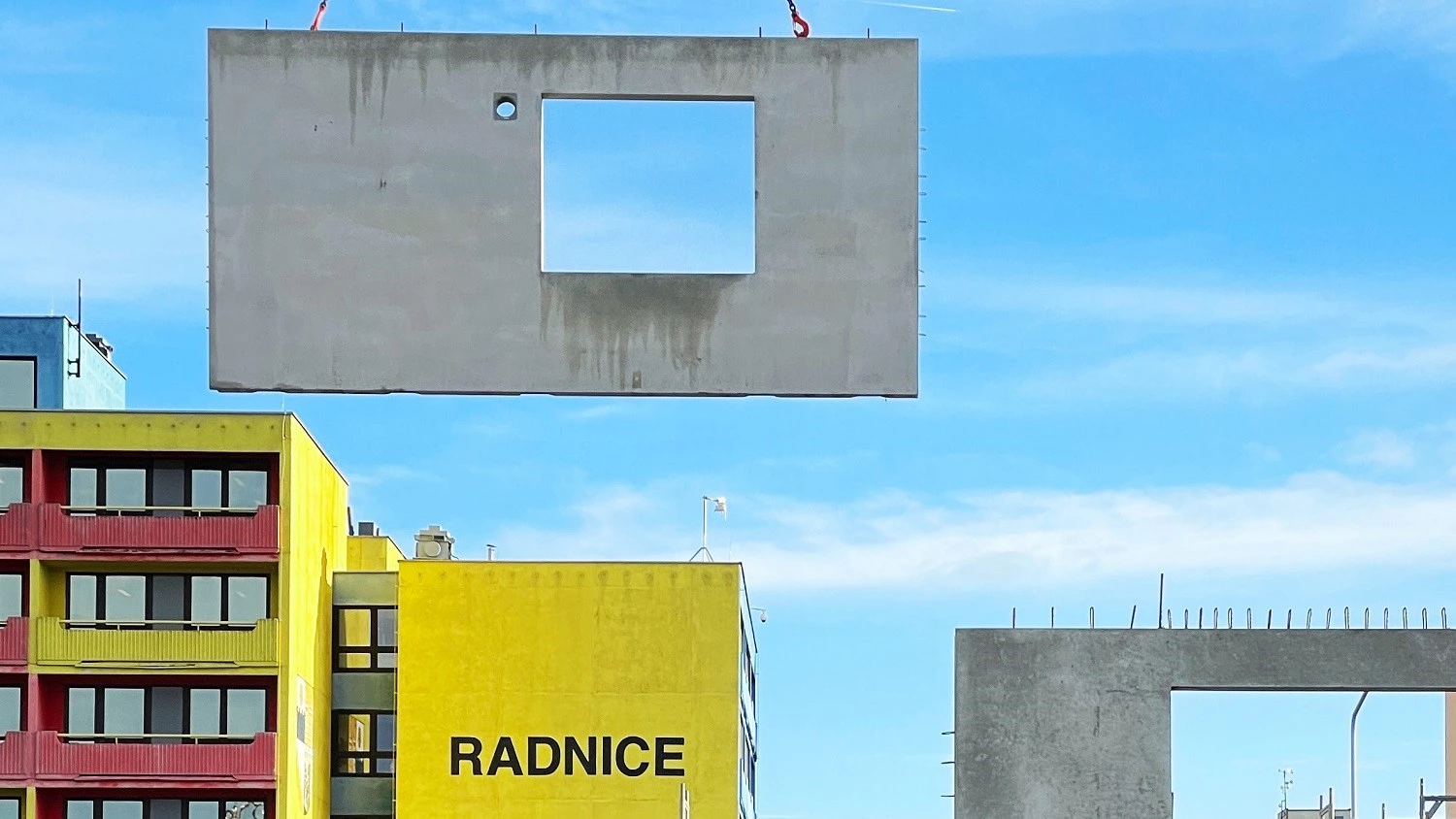
In 1.5 years, 275 modular bathrooms have been installed in YIT apartments in the Czech Republic. The developer is expanding the use of prefabrication to other building elements. By incorporating this technology, the company plans to not only improve the quality of its residential projects but also speed up their implementation. At the same time, it expects to have less demand for labour, which is in short supply. In addition to bathrooms, the developer is now also using modular manufacturing for structural elements. The Czech branch of YIT is following in the footsteps of its parent company in Finland, which has been building in this way since the 1970s, YIT told the press.
Construction from modules, so-called prefabrication, has its own specifics compared to the traditional one. Its principle is that ready-made modules are brought to the construction site (e.g. the entire future bathroom of the apartment, including fittings, tiles and tiles), were previously created in specialised production plants. On-site, they are then simply assembled by cranes into the skeleton of the building. Part of the work is thus carried out in the comfort of the factory, where the workers are not restricted by bad weather. "Prefabrication is, in our view, one way that can help to address the current unsatisfactory housing market situation. In addition to lengthy permitting processes, problems in the construction industry are hindering the construction of more housing. These have been exacerbated by the outbreak of the war in Ukraine, where material deliveries have either been significantly extended or stopped altogether. In addition, there is a long-term shortage of professional craftsmen and workers in the Czech Republic," explains Marek Lokaj, CEO of YIT Stavo, adding: "The potential of modular construction is huge and we want to make the most of it. Therefore, we have proceeded to further expansion, and in addition to bathrooms, we are installing other prefabricated structural elements in the Happi Milánská project - staircase arms, elevator shafts, balcony panels, ceiling filigree and now also wall panels.
YIT installed the first-ever bathroom in the autumn of 2019 in a model apartment in the eighth phase of the Pori residential complex Suomi Hloubětín. It has continued on a larger scale in the Kemi and Ranua phases of the neighbouring Lappi Hloubetin project, where more than 180 bathrooms have been installed so far. In the Vesi Hostivař complex, nearly 40 modules have already been installed, and in another project, Happi Milanská, 55 out of a total of 94 modular bathrooms have been installed so far. However, the developer also expects to significantly expand the use of prefabricated elements here. "The main advantages of modular construction include saving time, financial costs and labour. However, for a conventional project, we expect to speed up construction by around 1.5 months," says YIT Stavo Production Director Petr Altmann, adding, "In addition to conceptual solutions, we are also working on minor adjustments, such as reorganising the sequence of certain professions on site, including their local reinforcement at critical nodes. It turns out that even such seemingly subtle changes can result in additional time savings of more than a month. If our calculations prove correct, the reduction in construction time will also benefit new unit owners."
In Finland, modular elements for bathrooms began to be used as early as 1970. In residential construction here, YIT has so far completed around 15,000 elements, and its current annual volume is approximately 1,300 modules. It even incorporates the much sought-after saunas in some bathrooms. "Colleagues from Finland confirm that there are savings of around 2 months in the time schedule, while fewer foremen are needed on site. For example, on a Finnish 'conventional' construction site there is only a construction manager and three foremen, the use of modular bathroom elements reduces the need for just two," says Peter Altmann.