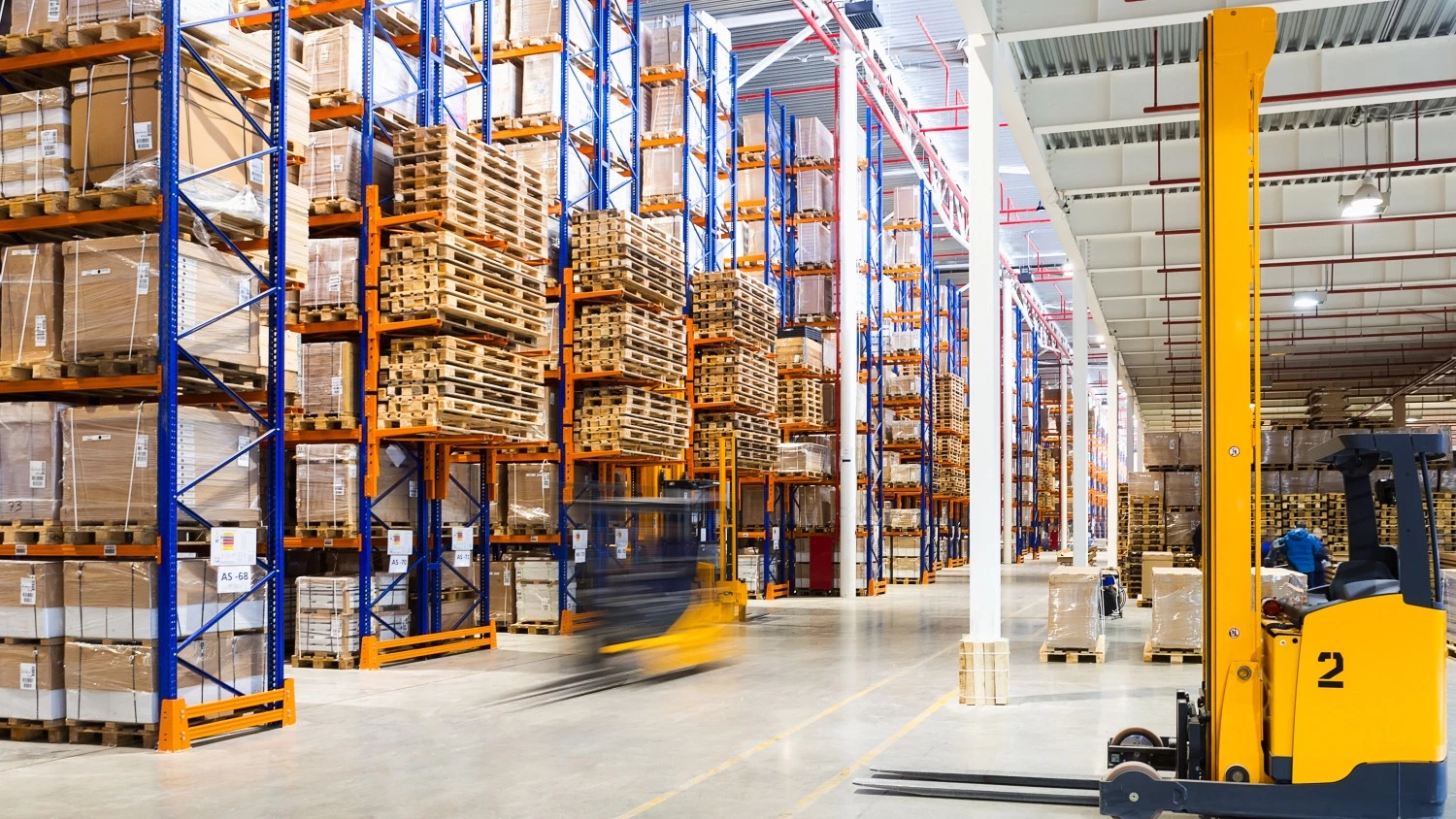
Warehouse occupancy costs are a broad concept that can be interpreted in many ways. The key components include rent and service charges. Utility charges billed according to individual consumption constitute a variable component. And on top of that, there are the costs of labour, logistics, supply chains and use costs of space itself. Tenants frequently forget that rent paid to the landlord is not the only cost of doing business in a warehouse facility. “A service charge is the maintenance cost of a facility that is often part of a larger industrial park - it is reinvoiced to individual tenants by the landlord. Its key component is the property tax levied on the landlord and determined by local municipalities,” says Daniel Kempa, Associate, Industrial & Logistics, Cushman & Wakefield.
Why do service charges differ?
The situation where the land on which the warehouse is situated is in perpetual usufruct is the least favourable to tenants as the service charge is much higher than in the case of freehold. Security and surveillance services for the property and the entire site are other major components of the service charge. The amount of this component - as in the case of taxes - is largely beyond the control of the landlord as it is chiefly influenced by the state-controlled minimum wage.
Service charges also include property insurance, technical supervision, maintenance of common areas such as greenery, roads, lighting, and removal of snow from rooftops. An important element that tends to be overlooked is the property manager’s fee accounting for up to 3% of the annual rent paid by the tenant. Warehouse occupancy costs also include utility charges billed according to individual consumption and comprising electricity, water, heating, and ITC and other technological services.
Lower warehousing costs? Look at the heating system and thermal performance of your building
How the warehouse is heated is important. Most warehouse buildings are heated by gas through infrared or air heaters. How gas is sourced is key then – is it mains gas or LPG, the latter being considerably more costly, with a knock-on effect on service charges for leased warehouse space.
Thermal performance is another aspect to be considered when leasing warehouse or manufacturing space – the better the heat transfer coefficient of a building, the lower the heating costs. Electricity consumption depends on space utilisation by the tenant. In the case of manufacturing tenants, electricity consumption will come from machinery, equipment, ventilation, air-conditioning and other systems. Manufacturers are increasingly opting for ventilation systems with heat recovery where heat generated by machinery and equipment is recovered and used, for instance, to heat office and welfare space, thereby generating considerable savings.
Although still rare, photovoltaic panels are mounted on rooftops of warehouse or manufacturing facilities to generate electric power for tenants’ needs. Unfortunately, the costs of such a system are still quite high due to both the price of the system itself and its installation and the cost of reinforcing the roof structure.
The location of a warehouse also impacts on occupancy costs
“The last category of warehouse occupancy costs could be called unobvious. It includes the location of a facility, the utilisation and optimisation of leased space. When leasing warehouse space, its location is key. There’s a real estate market saying that the three key features of a property are: “location, location, and location,” says Daniel Kempa.
The place of doing business has a tremendous impact on business operating costs. Transportation and labour costs could vary significantly depending on the location of the leased warehouse. The area of doing business, the target market, areas from which employees will be commuting to work and where to recruit new staff will all need to be factored in. The choice of the best warehouse location for business operations should be made with regard for the above factors.
Lower bills thanks to space optimisation
The utilisation of warehouse or production space and optimisation of its area will have an effect on the overall occupancy costs. Leased space should be effectively utilised - machines, racks and workstations should be spaced out optimally to prevent losses due to unused or empty spaces. As a result, you will lease only as much space as you actually need. Other factors to be considered include the clear height of the warehouse, racking systems and overall warehouse services.
What does warehouse rent include?
“Rent comprises multiple components that have a direct or indirect impact on the amount of charges paid for leasing warehouse space. Each project requires a case-by-case and comprehensive approach. As illustrated above, rent is not always equivalent to a service charge,” concludes Daniel Kempa, Cushman & Wakefield.